Back in September, we learned how to separate sheep and wool. In August it was cotton. There was also linen, bamboo, alpaca, angora and on and on. But then what? How does that mass of matty, filthy, greasy, smelly fiber transform into clean, tidy, brilliantly colored yarn?
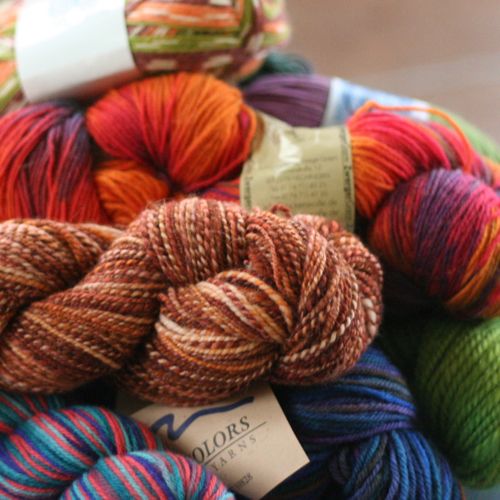
I bet you thought you’d never find out. This article only hits the highlights – what I left out could fill a library!
The basic steps in fiber processing are the same for any natural fiber:
- Wash – Fiber comes from outdoors. Outdoors is filthy.
- Pick – Separate the fiber so it’s loose and not clumpy. Larger bits of nature are removed. Commercial yarns are typically ‘scoured’ as well; they are treated with a chemical that burns out any organic material.
- Card – Brush brush comb comb. Lines up the individual fibers.
- Roving – Roll the fiber into a fluffy, loose, soft rope.
- Spin – Twist up that roving! Spinning adds firmness and stability. Strands are twisted together for additional structure, different weights and appearance. Each individual strand is called a ‘ply’. The more plys – the sturdier the yarn. The number of plys does not necessarily indicate the weight of the yarn!
- Wind/Skein/Ball – Yarn is put into a usable amount and workable format.
In the case of large yarn companies, these steps may all happen in a different places – possibly in different locations around the globe. There are also smaller spinneries who do everything in-house and provide custom services (Ohio Valley Natural Fibers), local spinneries that combine and process all the fleece (or whatever) in their general area (Green Mountain Spinnery), certified organic spinneries (Vermont Organic Fiber Co.), wind-powered fiber mills (Hope Spinnery) and on and on. In the past few years, it seems like there are more small local mills than ever. I think it has to do with the internet. These unique yarns have been given a broader marketplace than a fiber festival and have become more financially viable. And of course, fiber can be processed and spun by hand!
Commercial processing uses lots of chemicals to condition, bleach, soften or moth-proof the fiber as well as make it easer to process. Commercial processing is also heavy on water use. Organic processing uses different combinations of organic agents and biodegradable soaps to limit environmental impact. ‘Natural processing’ also indicates that less chemicals are used (sometimes only soap). So if you want an environmentally friendly yarn look for: organic, minimally processed, mills that use alternative power sources and are conscious about water use (clean it, treat it, recycle it). For a yarn to be labeled as ‘organic’ after processing, it must be grown and processed, dyed to organic standards and have the paperwork to go with it. A yarn labeled as ‘organically-grown’ or ‘organically-processed’ is only that – it could be dyed with anything. If you purchase hand-processed yarn, there may be little bits of grass and stuff spun in. This indicates that the yarn has not been chemically scoured (a good thing) just pick it out as you knit.
For a closer look at fiber processing in a mill setting, the following is a really great video from Autumn Mist Alpaca Farm in New York. It’s almost 15 minutes long but worth it if you’ve got the time.
She does indeed say that she’s de-hairing dog fur.
Now, dyeing. Every type of fiber responds to color differently. Every type of dye reacts differently to fiber. There are acid dyes, basic dyes, reactive dyes, sulfer dyes, vegetable dyes, people even dye yarn with Kool-Aid. Natural dyes (made from plants) take a lot a LOT longer than the chemical type and the colors aren’t as vibrant. Some yarns sit in their nautral dye baths for days or weeks to achieve the desired saturation. There are many variables that affect the color during the process: water temperature, age of the dye, agitation, fiber type, preparation, time in the dye, colorant to water to fiber ratio and on and on. There are also many many many ways of getting dye onto the fiber: squirt bottles, spray bottles, dipping, dunking, boiling, microwave, paint brushes. But there are only two basic times during processing sequence that dye is applied: after the yarn is spun (dyed in the yarn) or while the fiber is still, well, fiber (dyed in the wool).
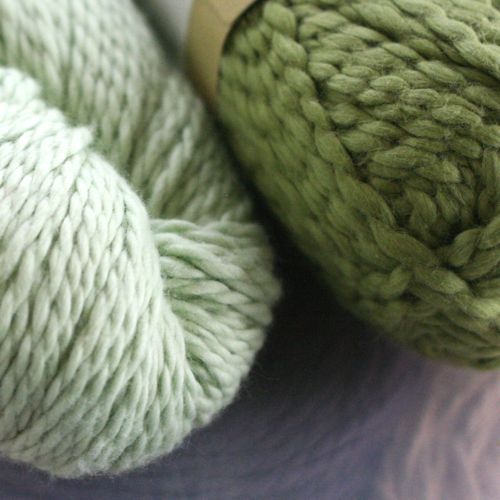
Left: conventional acid dye / Right: organic vegetable dye
The immersion method of dying is the most widely used method of dyeing ‘in the yarn’. Basically, hanks of yarn are dunked in vats of dye. There are dozens of different ways to dunk the yarn (by machine or by hand) and an infinite number of sizes of vat. The ‘lot’ is how many skeins fit into the vat at one time. On an industrial scale, immersion lots dyed with acid dyes stay intense and true in color from one skein to the next. Hand-processed lots vary more within the lot.
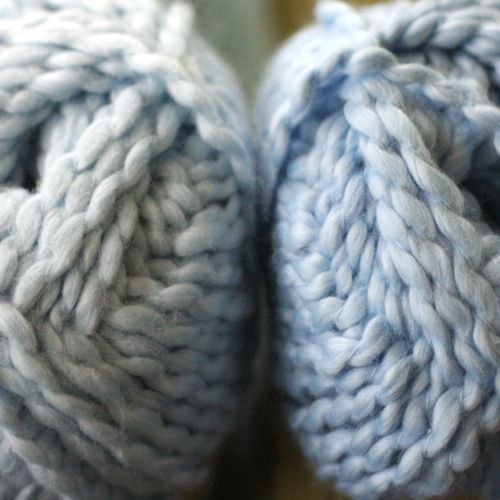
Same color, different lots. (vegetable dye)
To ‘dye in the wool,’ the raw and fluffy fleecy poof is treated with dye before it’s ever spun. Some crazy things can be done with color: heathered yarns, blending red and yellow fiber to make orange, spots, stripes, unique and unrepeatable variations. Look for yarns labeled ‘dyed in the wool’, ‘fleece dyed’ or ‘stock-dyed.’
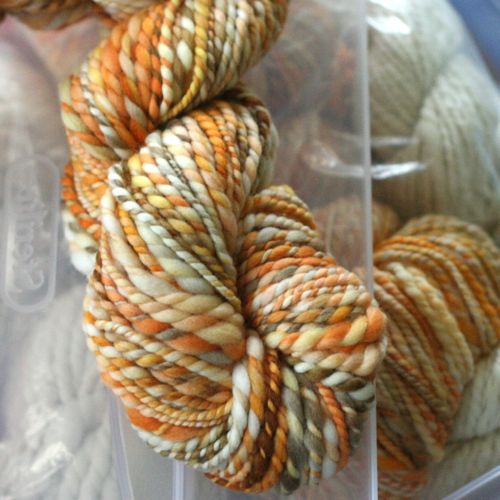
Roger’s yarn is dyed as roving, spun and then plied with another strand.
Interestingly: when you buy yarn from a small hand-dyed yarn company – particularly one-person operations – their undyed, millspun yarn typically comes from the same yarn suppliers as everyone else’s (ie Henry’s Attic, Louet). Because of that, the dyer’s eye for color, application and type of dye is the differentiator.
If you want something entirely unique, look for yarns that are hand spun and hand dyed. Myrtille of SpinSpanSpun creates exactly that. I found Myrtille when I was looking for a custom heavy-weight yarn for C is for Cat and I have drooled over her wares ever since! SpinSpanSpun carries a great mix of mill and hand spun yarns a large chunk of which is organic wool from the French Alps. When superior materials and Myrtille’s talent for color are combined, the result is simply marvelous. Myrtille lives in France, so it takes a bit for the yarn to make it from her door to mine but every moment is worth it. Just ask her Ravelry group and her Etsy customers. For our giveaway this month, I have eleven of Myrtille’s miniskeins!
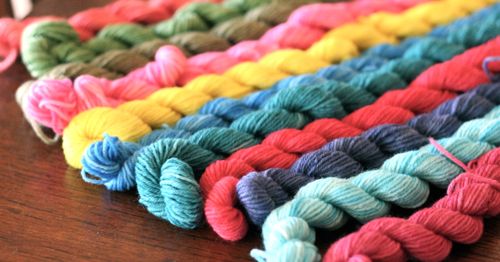
Mill spun organic merino sock weight dyed with eco-friendly dyes.
They’ll be perfectly perfect for Meg Hollar’s 7 Colorwork Christmas Ornaments!
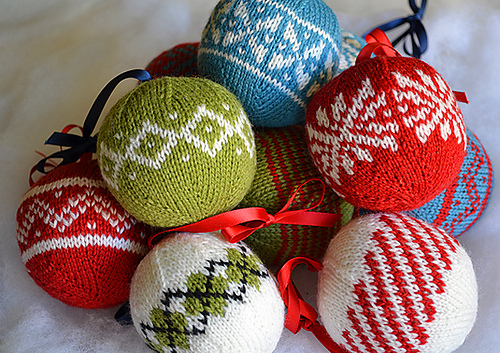
That’s Meg’s picture – used with permission.
The yarn will come (from Alabama, not France) by Priority Mail and the pattern by Ravelry gift (you don’t have to Ravel). If colorwork (or Christmas) isn’t your thing, you can get four hexi-puffs out of each skein.
Whatever you choose to make, comment on this post with all haste! Since it worked so well last time, extra entries for those who post, retweet, pin or whatever! Please leave another comment for counting purposes. We’ll leave this giveaway open for just one week – until December 4, 2012 so that the winner has time to make ornaments!
They’re small. And I am sure y’all can knit like the wind.